Understanding Respiratory Protection
Fit testing will determine if your mask is providing the protection you need to stay safe.
Protection through Respiratory Fit Testing & Training
A Respirator fit test is required to meet AS/NZS Standards
The Australian Standard AS/NZS 1715 S2(2.6) requires Respiratory Protection Equipment (RPE) users with a close-fitting facepiece to carry out a suitable fit test at least once per year.
What is fit testing?
Respirator fit testing uses a ‘PortaCount’ machine to measure how much air is leaking from a respirator when an individual wears it. This approach enables us to use an objective quantitative method to assess whether the respirator provides an adequate face seal and the required protection.
Quantitative vs. Qualitative?
A PortaCount quantitative fit test eliminates subjectivity. Rather than depending upon a person’s chemical sensitivity or cooperation, a quantitative fit test measures actual fit and determines if the mask has achieved an adequate face seal.
In addition, a PortaCount fit test measures fit while the user simultaneously performs a series of moving, breathing, and talking exercises. This approach simulates the movements made in the workplace.
Our clients receive clear evidence and documentation as a result of a quantitative respirator fit test. We can provide fit test results for each employee, ensuring our clients maintain compliance with the national standard.
Some reasons a Quantitative Fit Test could fail include:
- Size: Incorrect size mask for the wearer
- Age: Masks will deteriorate over time and require periodic replacement
- Condition: Poor storage, incorrect donning/doffing technique, and lack of maintenance may lead to premature aging
- Strap tension: Uneven strap tension or over-tightening may cause a poor seal or slippage of the mask on the wearer
- Facial features of the wearer: Bone structure or facial hair can cause leakage around the seal.
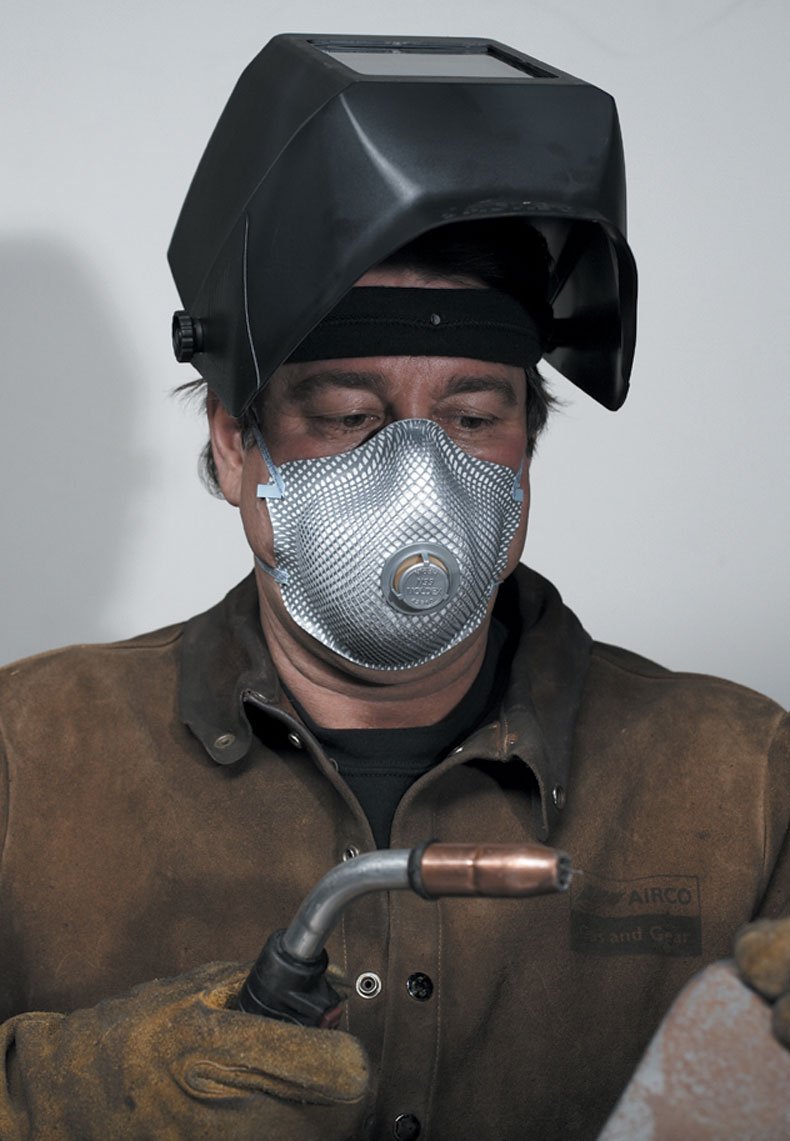
THE PROTECTION FACTOR OF ANY RESPIRATOR CANNOT BE RELIED UPON UNLESS YOUR MASK HAS BEEN FIT TESTED
Respiratory Protection Guidelines
The Australian Standard, ASNZS/1715 Selection, Use, and Maintenance of Respiratory Protective Equipment, sets out guidelines of respiratory protection requirements. The standard includes recommendations for selecting, using, and maintaining Respiratory Protective Equipment (RPE) in the workplace. To comply with AS/NZS 1715:2009 you require a respiratory program in place covering the following:

- Appointing a programme administrator
- Selection of RPE
- Medical screening of end users
- Training
- Issue of RPE
- Fitting of RPE
- Testing of RPE
- Wearing of RPE
- Maintenance of RPE
- Record keeping
- Programme evaluation
Further explanation of the above program components
-
Appointing a program administrator – S2: (2.2)
It is mandatory to appoint a program administrator. The administrator is responsible for completing the requirements set out in the guidelines.
-
Selection of RPE – S2: (2.3)
RPE needs to be worn whenever a person is exposed to excessive levels of contaminant. Factors for selection include:
- Contaminant
- Task at hand
- Operator
- Equipment limitations
- Special response HAZMAT incidents
- Only RPE complying with AS/NZS 1716:2012 should be used.
-
Medical screening of end-users – S2: (2.3)
Before use, all RPE users should have an initial medical assessment. Take physiological considerations into account. For instance, an effort is required to breathe through some respirators. Assess people with cardiac or respiratory disorders and consider other factors such as heavy work, prolonged use, and physical features such as facial hair (that could break the seal on a mask). Enclosed RPE, such as hoods, helmets, or full face masks, may give rise to feelings of claustrophobia, isolation, and anxiety in some people.
-
Training – S2: (2.4)
A competent person should provide training. The training should include:
- Identification of the hazard/s
- Reasons for the RPE
- RPE selection
- Use and proper fitting of RPE
- Wear time
- Limitations of RPE
- Maintenance and storage
- Summary of the workplace respiratory protection program.
-
Issue of RPE – S2: (2.5)
Where practicable, RPE should be issued for the exclusive use of the wearer, wherever practicable. Keep records documenting the issue, provision of consumables, and maintenance. Filters need to be marked with the date of issue and user ID. Non-personal RPE must be cleaned before reuse.
6 & 7. Fitting and testing of equipment – S2: (2.6 & 8.5)
All RPE requiring a close-fitting facepiece needs to be properly fitted and sized to the wearer. The standard requires users to have an annual fit test. There are two types of facial fit tests:
- Qualitative: is subjective, as may be influenced by the wearer
- Quantitative: is not subjective, suited to all mask types, and requires a trained operator. Full face respirators have to be tested with this method to obtain complete protection.
-
Wearing of RPE – S2: (2.7)
The respiratory program ensures RPE is worn and fitted correctly and used when and where required.
-
Maintenance of RPE – S4: (2.8)
PRE maintenance should follow the manufacturer’s instructions including,
- Cleaning and disinfection
- Inspection to check equipment is in working order
- Repair and replacement of components (including filters)
- Correct storage
- Disposal of worn/expired masks and components.
-
Record keeping – S4: (2.9)
Records for a respiratory programme should include:
- Issue date of RPE,
- User records: Training, fit test, medical screening
- Filter replacement schedule,
- RPE maintenance schedule
- Programme records: Procedures, audits and evaluations, atmospheric monitoring records, health surveillance
-
Programme Evaluation
Audit the respiratory protection program at least once per year. Make adjustments to the program based upon the evaluation results.
Do you have a documented filter replacement Schedule?
AS/NZS 1715:2009 requires a reported filter replacement schedule to be in place for each work task. Base the schedule on the manufacturer’s guidelines. Replacement time will vary significantly based upon:
- Concentration levels of a contaminant in the atmosphere
- Lung Capacity and breathing rate of the worker
- Humidity
- Length of time filter is in use.
Some reasons a Quantitative Fit Test could fail:
- Size – Incorrect size mask for the wearer
- Age – Masks will deteriorate over time and require periodic replacement
- Condition – Poor storage, incorrect donning/doffing technique, and lack of maintenance may lead to premature aging
- Strap tension – Uneven strap tension or over-tightening may cause a poor seal or slippage of the mask on the wearer
- Facial features of the wearer – Bone structure or facial hair can cause leakage around the seal
Date your cartridges on opening
- You can identify the replacement time/date based on your replacement schedule.
- Supervisors/managers can easily see when a replacement is coming up.
AS/NZS 1715:2009 – cartridges come in a sealed package, and, once opened, their use should not exceed six months,
Resource Acknowledgement: MOLDEX-METRIC International www.moldex.com